Create a Daily Inspection Checklist for Preventing Overhead Accidents
- Posted on
- By SWSS
- 0
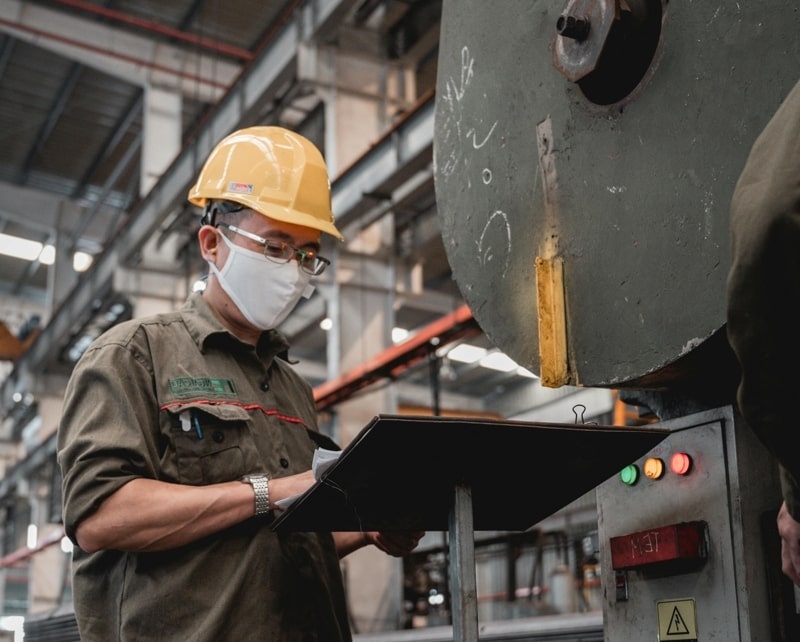
A busy factory floor often includes heavy loads that move overhead, and sometimes a single lapse in attention to detail can lead to serious harm. Things as simple as a hoist accidentally dropping its cargo can severely damage valuable equipment, just because a crucial part in the apparatus was worn down.
Accidents can be substantially reduced with daily inspections. They help to maintain safe operations because they catch issues before they escalate. A consistent checklist protects both employees and productivity by addressing potential hazards in a structured way and before they happen.
The Importance of Daily Hoist Inspections
Hoists in a factory environment handle significant weight on a regular basis - like overhead crane hoists - and they require routine checks for overall reliability. Without routine checks, equipment will eventually fail and can cause serious injury, downtown and loss of revenue.
You maintain safer workflows when you identify mechanical problems early, so be aware that daily inspections encourage employees to take note of minor abnormalities that could grow into major setbacks.
Also, management can reduce expensive repairs because consistent inspection routines catch signs of corrosion or loose components and rectify them in a timely manner.
Identifying Early Wear and Tear
Hoists contain gears, hooks, chains, and other parts that need regular and careful scrutiny. With a little elbow-grease, you can discover cracks, bends, or weakening links when you conduct daily observations.
Remember that even minor deterioration can compromise load-bearing capacity, especially when workers are under time pressure. Preventive measures start with close visual analysis of structural components because small failures may trigger large accidents in the short or long term.
Preventing Costly Downtime
Equipment shutdowns slow your production output and lead to lost revenue for the entire operation, but daily inspections shorten unplanned downtime because they allow teams to schedule maintenance before a breakdown occurs.
Factories that schedule routine inspections protect their employees from hazardous incidents and preserve efficient workflows. Keep in mind that overhead accidents are disruptive because they create safety concerns and damage factory resources.
These checks create a dependable foundation that upholds safety and productivity in equal measure.
The next step involves creating a precise checklist, which organizes these observations into a more structured form.
Build an Effective Hoist Inspection Checklist
A documented checklist leads to consistent and thorough hoist examinations. It provides a reference point that employees can follow without missing critical elements during their shifts.
Take note that every factory has unique requirements, so your checklist should address the specific machinery and procedures used on site. Consider creating a well-crafted list to ensure uniform reporting practices because it establishes a shared standard for evaluating hoist conditions.
Perform Essential Visual Checks
Your daily walkthrough should include careful observation of hooks, latches, chains, and wire ropes. Consider that a concise bullet list clarifies these checks:
- Inspect hooks for cracks
- Confirm latches fasten securely
- Check chains for rust or misalignment
- Examine wire ropes for fraying or kinks
An example is crane chain hoists. Crane chain hoists benefit greatly from daily inspection routines, because they are vigorously used on a daily basis and regular lubrication and chain alignment checks will help prevent unexpected malfunctions.
Bear in mind that a stable hoist requires intact hardware because compromised parts can trigger serious hazards.
This is a structured approach to safety that assists teams in spotting early damage before heavier workloads intensify the risk.
Setup Functional Testing Procedures
Operators can run a hoist through simple load-lifting trials to check responsiveness and stability. They simply observe any unusual vibrations or jerky movements that indicate internal damage. They should be aware that a short operational test will uncover hidden faults by revealing performance abilities under slight stress.
You bolster overall safety when you address these concerns well before heavy loads are involved.
Proper documentation of visual and functional observations should be done to reduce future human error because it encourages clear communication.
With a solid checklist like this in place, it becomes vital to promote accident prevention through well-defined practices.
Promote Accident Prevention in Overhead Operations
Factories must focus on a comprehensive approach that unites equipment-checks and employee training programs. Workers gain confidence when they see management taking active steps to safeguard their well-being.
Daily hoist inspections blend effectively with broader safety policies that cover topics such as wearing proper work clothing, stocking essential first aid items, and ensuring head safety while on the work site or the floor.
This type of procedural alignment will continually remind employees to recognize that protective measures extend beyond a single device and include a wide range of site-specific precautions to be put in place.
Launch Teamwide Safety Training Sessions
Supervisors can organize frequent workshops to ensure workers understand correct hoist operation, inspection methods and overall safety precautions.
Regular interactive demonstrations reinforce best practices because they allow individuals to see real examples of safe lifting techniques.
Teamwide education sessions also reduce confusion and fosters a sense of accountability.
Ensure Consistent Equipment Maintenance
Scheduled servicing maintains components in good condition because it handles routine wear before it worsens.
Mechanics can do things like regularly lubricate moving parts and replace damaged pieces right away, to extend the hoist’s lifespan.
Consistent maintenance works best when it's backed by daily inspection data that pinpoints troubled areas without delay.
Schedule maintenance keep operators engaged in safety when they see that leadership invests a lot of time in well-maintained machinery.
The final step is to strengthen your workplace safety culture with specific actions that reinforce daily inspections and promote continuous improvement.
Strengthen Your Workplace Safety Culture
A factory thrives on dependable systems that protect workers and ensure smooth operations. To keep things running smoothly, you can encourage employees to integrate daily hoist inspections into their routines because consistent follow-through demonstrates commitment to collective well-being.
Remember that overhead accidents can have serious consequences, which highlights the importance of thorough planning. When you unify your inspection plans with other precautionary measures, you keep your head safe on the worksite, and maintain a robust shield against potential hazards.
Reinforce Accountability Measures
Company leaders can track inspection compliance by reviewing checklists and requesting feedback from operators. This strategy instils a culture of ownership because every person begins to understand the value of consistent reporting.
Management can also recognize individual achievements when employees catch and correct minor flaws early and report them. Acknowledgment of proactive behaviour will foster a sense of pride and cooperation among your entire team.
Research Additional Resources
Industry experts offer valuable insights on evolving best practices for overhead equipment. Official regulations help shape your policies, and they enhance your factory’s approach to accident prevention.
By keeping communication channels open, you'll be able to gather new ideas and update your processes regularly.
Comments
Be the first to comment...